FACHGLOSSAR
Kontaktieren Sie uns
Eine Form ist eine Ausrüstung, die aus zahlreichen Komponenten besteht, die sich sowohl im Material als auch in der Geometrie unterscheiden, und das ein Teil gemäß den Spezifikationen reproduzieren muss.
Die wichtigsten Merkmale dieser Art von Formen sind die Notwendigkeit, sehr hohen Temperaturen, mechanischen, chemischen und physikalischen Belastungen standzuhalten.
Die traditionelle Form besteht aus zwei Teilen: einem festen und einem beweglichen Teil.
Eine Druckgussform besteht in der Regel aus verschiedenen Teilen, die jeweils spezifische Eigenschaften und Funktionen haben; hier einige der wichtigsten Komponenten:
- Matrizen: Sie sind in der Regel in zwei Teile unterteilt (beweglich und fest) und bilden das Negativ der herzustellenden Form (des Teils). Die Matrizen werden durch spanabhebende Bearbeitung oder Erodieren hergestellt, um die geometrische Form des Bauteils zu erhalten. Es gibt auch eine Reihe von Löchern, welche die Temperaturregelkreise bilden. Die Matrizen werden dann wärmebehandelt, um den richtigen Härtegrad und die richtige Widerstandsfähigkeit gegen Heißverschleiß zu erhalten.
- - Formeinsätze: Es gibt Situationen, in denen übermäßiger Verschleiß aufgrund der Geometrie des Teils und der Bedingungen, unter denen die Werkzeuge eingesetzt werden, zu begrenzten Bereichen in der Matrize führt, so dass Teile hergestellt werden müssen, die in die Matrizen eingesetzt werden. Diese Einsätze müssen leicht zu ersetzen und zu warten sein, haben im Allgemeinen eine kürzere Lebensdauer als die Matrize und müssen häufiger gewechselt werden.
- Bewegungen: Einige Teilegeometrien können Bereiche aufweisen, die einen Druck nur durch zusätzliche Bewegungen zum Öffnen der Druckplatten möglich machen. Diese Bewegungen dienen dazu, die so genannten 'Hinterschneidungen' in dem zu produzierenden Teil freizulegen. Es gibt drei Haupttypen von Bewegungen: mechanisch, hydraulisch oder gemischt.
- Formhalterung: Besteht in der Regel aus zwei Teilen (beweglich und fest) und hat die Aufgabe, die Matrizen aufzunehmen. Sie müssen so konstruiert sein, dass sie eine möglichst bequeme Wartung der in ihnen eingebauten Komponenten ermöglichen und eine langfristige strukturelle Solidität für die Massenproduktion gewährleisten.
- Gerüst: Die Hauptfunktion ist die Aufnahme der Platten, welche den Auszug der Teile ermöglichen, sowie das Einspannen der Form in die Produktionspresse und das Tragen der mobilen Formhalterung.
- Auszugstische: Ihre Funktion ist es, die Auswerfer zu bewegen, um das produzierte Teil von der Form zu trennen. Manchmal können sie auch "Höcker"-Sektoren bewegen, um Hinterschneidungen von begrenzter Größe in der Figur zu beseitigen.
Das heiße Kammer-Druckgussverfahren für Metalllegierungen, auch bekannt als 'Spritzguss', ist gekennzeichnet durch einen in die Druckgussmaschine integrierten Schmelzofen und eine in den Tiegel eingetauchte Einspritzvorrichtung. Diese Methode ermöglicht kürzere Zykluszeiten, eine bessere Temperaturkontrolle und ein geringeres Risiko der Legierungsoxidation, ist aber aufgrund ihrer Konstruktion nur bei niedrig schmelzenden Legierungen möglich. Sie ist daher für Legierungen geeignet, die sich durch eine Schmelztemperatur unter 450°C auszeichnen, wie z.B. Zink- und Bleilegierungen, während sie für Aluminium- und Magnesiumlegierungen, welche die Einspritzvorrichtung übermäßig verschleißen, nur unter besonderen Bedingungen verwendet werden kann.
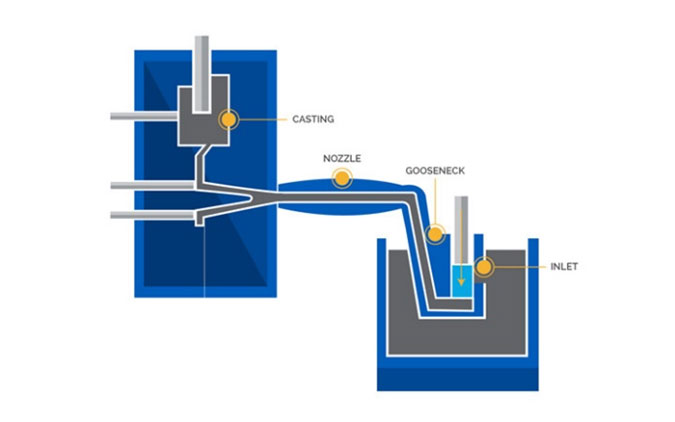
Es gibt zwei Haupttypen des heiße Kammer-Druckgusses:
- KOLBENSCHIEBEN (am häufigsten): Das Material gelangt über einen Durchgangsbereich in die Einspritzvorrichtung und wird dank der vertikalen Bewegung des Kolbens eingespritzt, der die Legierung entlang der Kanäle schiebt, bis der/die Formhohlraum/e gefüllt sind.
- OSZILLIERENDE DRUCKKAMMER (weniger gebräuchlich): Die Kammer füllt sich durch Kippen, während der Strahl abgesaugt wird. Sobald die Form geschlossen ist, kehrt sie in ihre Position zurück und ermöglicht das Einspritzen durch die Wirkung der Druckluft auf die Oberfläche des flüssigen Metalls.
Das kalte Kammer-Druckgussverfahren für Metalllegierungen, auch bekannt als 'Druckguss', zeichnet sich durch eine Einspritzvorrichtung aus, die völlig unabhängig vom Schmelzofen ist. Diese Methode senkt die Wartungskosten und ermöglicht vor allem höhere Einspritzgeschwindigkeiten und -drücke. Außerdem ist sie für bestimmte hochschmelzende Legierungen wie Aluminium und Magnesium unerlässlich.
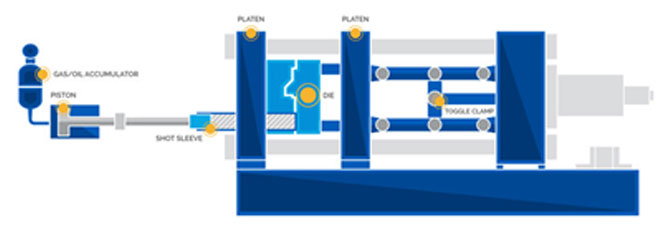
Die Metalllegierung wird, nachdem sie in den Einspritzzylinder gegossen wurde, durch die Wirkung eines Zylinders in drei Schritten durch die Düse in den Hohlraum gedrückt:
- 1. PHASE (Vorfüllen): mäßige Geschwindigkeiten und Drücke, um den Lufteintrag zu minimieren, bis die Gussverbindungen erreicht sind.
- 2. PHASE (Füllen): erhöhte Geschwindigkeiten und Drücke, bis der Hohlraum vollständig gefüllt ist.
- 3. PHASE (Nachdruck): weitere Erhöhung des Drucks und Aufhebung der Geschwindigkeit, um die Verfestigungsschrumpfung auszugleichen.
Das Thixomoulding-Verfahren für Magnesiumgranulat besteht darin, Magnesiumgranulat in einen Trichter einzufüllen, bis eine volumetrische Sättigung in Gegenwart von Argon erreicht ist. Während der Einspritzphase durchläuft das Granulat eine Zone, die durch das Vorhandensein einer Schnecke gekennzeichnet ist, die, indem sie das Material einer Scherbeanspruchung aussetzt, die in der flüssigen Phase vorhandenen Dendriten zertrümmert (die Vorsilbe 'Thixo' weist auf das Vorhandensein eines Feststoffanteils von mehr als oder gleich 50% hin) und dabei kugelförmige Partikel in einem halbfesten, thixotropen Zustand erzeugt, d.h. die in der Lage sind, durch mechanische Bewegung, die durch Einspritzen in den Formhohlraum erfolgt, flüssig zu werden.
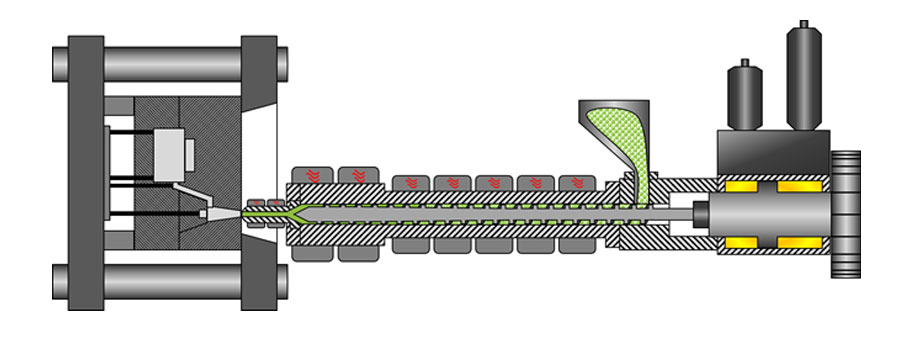
Die Hauptvorteile dieses Verfahrens liegen in der gleichachsigen Struktur der erhaltenen Gussteile sowie in der Wiederholbarkeit, der Komplexität und der Kontrolle der produzierten Teile, welche die Herstellung von "Near-Net-Shape"-Gussteilen ermöglichen (in der Nähe der vom Projekt vorgegebenen Form). Außerdem eignet es sich besonders gut für Magnesiumlegierungen, da diese nicht in den geschmolzenen Zustand gebracht werden müssen und somit nicht mit der Luft in Berührung kommen können.
Das Spritzgussverfahren ist ein Produktionsverfahren, das industriell für die Herstellung von thermoplastischen Polymerprodukten verwendet wird. Konkret wird das Material auf eine Temperatur gebracht, bei der es plastifiziert und unter hohem Druck in den Formhohlraum gespritzt werden kann.
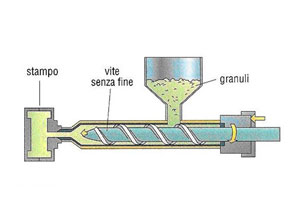
Das Funktionsschema des Prozesses, wie es in der Abbildung zusammengefasst ist, zeichnet sich durch einen Trichter aus, in den das Material in Form von Granulat eingefüllt wird. Die Schlüsselkomponente des Gussverfahrens ist die Schnecke, die zwei Hauptbewegungen hat:
- Drehung um seine Achse: Diese Bewegung, zusammen mit der thermischen Energie, die von einer großen Anzahl von Widerständen entlang des Zylinders bereitgestellt wird, ermöglicht die Plastifizierung des Polymers;
- Vorschub: Ermöglicht das Einspritzen der Polymerschmelze in den Formhohlraum für die Herstellung des Teils.
Die letzte grundlegende Komponente ist die Form, die das Polymer formt und aus der das Teil entnommen wird, sobald das Material verfestigt und ausreichend abgekühlt ist.
Thermoplastisches Einmaterial-Spritzgussverfahren
Das thermoplastische Einmaterial-Spritzguss wird durch das oben beschriebene Formverfahren realisiert und zeichnet sich durch die Verwendung eines einzigen Polymertyps zur Herstellung des endgültigen Teils aus. Es ist die einfachste Art der Formgebung, die durchgeführt werden kann, und hat kürzere Zykluszeiten als die anderen, da sie nicht durch Einspritzungen verschiedener Polymere, Gase und andere Merkmale beeinflusst wird, die sowohl die Komplexität als auch die Dauer der Prozesse beeinflussen. Auf der anderen Seite ist es jedoch schwierig, eine ästhetische und strukturelle Leistung zu erzielen, die für bestimmte Arten von Teilen geeignet ist. Insbesondere bei der Verwendung von Polymeren wie 'Commodities' (vor allem PE und PP) ist die mechanische Leistung der erhaltenen Teile bescheiden und es können Probleme wie Schrumpfung und Schrumpfung auftreten, die das Aussehen der Produkte beeinträchtigen und den Bereich der mechanischen Anwendung weiter einschränken, insbesondere in Sektoren wie der Automobil- und Luftfahrtindustrie. Durch die Verwendung von technischen Polymeren oder mit Additiven gefüllten Polymermaterialien ist es jedoch möglich, die Leistung im Betrieb zu verbessern, wobei das Design und die Wahl des richtigen Füllstoffs eine Schlüsselrolle spielen.
THERMOPLASTISCHES MEHRMATERIAL-SPRITZGUSSVERFAHREN
Das thermoplastische Mehrmaterial-Spritzgussverfahren ist im Gegensatz zum Einmaterial-Spritzgussverfahren eine Art des Spritzgießens, die durch die Verwendung mehrerer unterschiedlicher Materialien in Bezug auf die mechanischen und chemisch-physikalischen Eigenschaften gekennzeichnet ist. Im Vergleich zum Einmaterial-Spritzgussverfahren sind die Komplexität und die Dauer des Prozesses sicherlich höher und erfordern eine spezifische Optimierung des Gießzeitpunkts der einen oder anderen Düse, was manchmal komplexe Lösungen sowohl für die Maschine als auch für das Werkzeug erfordert. Es gibt verschiedene Möglichkeiten in diesem Bereich:
Doppel-Material-Spritzgussverfahren 2K: Dieses Spritzgussverfahren zeichnet sich durch das Vorhandensein von zwei verschiedenen Materialien aus und ermöglicht die Herstellung von Teilen mit hohen ästhetischen, dichtenden und leistungsfähigen Eigenschaften. Diese Eigenschaften sind eine notwendige Voraussetzung für strukturelle Anwendungen, z.B. im Automobilbereich. Die Verbindung der beiden Materialien wird durch die Temperatur und das Studium der Molekularchemie der verschiedenen verwendeten Polymere erreicht, so dass sie sowohl hohen Temperaturen und Drücken als auch den atmosphärischen oder umweltbedingten Einflüssen, die im Betrieb auftreten können, standhalten können.
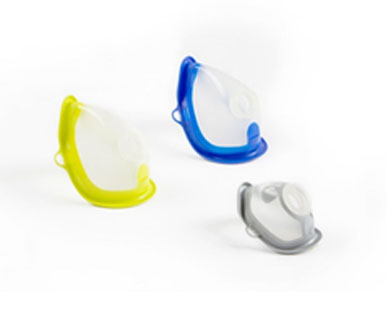
3K-Trimaterial-Spritzguss: Das Formteil zeichnet sich durch das Vorhandensein von drei verschiedenen Materialien aus, die es ermöglichen, äußerst technische Teile oder mit besonderen Anforderungen aus ästhetischer Sicht zu erhalten. Eine weitere wichtige Anwendung ist die Erstellung von Artefakten mit unterschiedlichen Farben im Inneren.
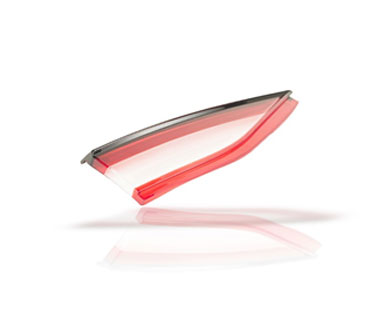
CO-SPRTITZGUSSVERFAHREN (INSERT MOULDING)
Insert Moulding oder Co-Spritzguss ist ein Formgebungsverfahren, bei dem polymeres Material in einen Formhohlraum eingespritzt wird, in dem bereits Einlegeteile oder Substrate positioniert sind, die für die Herstellung des endgültigen Teils erforderlich sind. Der Hauptzweck dieser Technik besteht neben der Möglichkeit, Teile zu produzieren, die auf andere Weise nur schwer zu erhalten sind, darin, die auf die Formgebungsphase folgenden Arbeitsgänge wie Endbearbeitung und Montage erheblich zu reduzieren, was eine Verringerung der Gesamtzykluszeiten ermöglicht und den Prozess automatisiert. Die Arten von Einsätzen können unterschiedlich sein oder aus verschiedenen Materialien bestehen (andere Polymere, Metalle, keramische Materialien usw.) und haben in der Regel vorbearbeitete Oberflächen, die das Anhaften des Materials während der Formgebungsphase erleichtern: ein klassisches Beispiel sind Gewindeeinsätze aus metallischem Material.
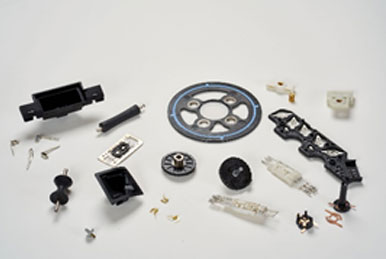
GASUNTERSTÜTZTES SPRITZGUSSVERFAHREN (GIM)
Das gasunterstützte Spritzgussverfahren, auch bekannt als GIM oder GAIM, ist eine Art des Spritzgießens, bei der in den letzten Phasen ein unter Druck stehendes Gas verwendet wird, welches das Material gegen die Wände oder das Ende der Form drückt. Die grundsätzliche Methodik ist die gleiche wie beim klassischen Spritzguss, aber wenn das Material etwa 80% des Hohlraums gefüllt hat, wird Gas durch eine Reihe speziell entwickelter Einlasskanäle insuffliert, das die oben genannten Funktionen erfüllt. Mit dieser Technik ist es möglich, sowohl das Gewicht als auch die Kosten der hergestellten Teile zu reduzieren und Hohlkörper mit größerer Dicke, geringerer Verformung und weniger Oberflächenansaugung zu erhalten. Es gibt jedoch auch Nachteile, insbesondere bei Formen mit mehreren Hohlräumen: Es ist nämlich nicht einfach, geeignete Kanäle und Installationen für das Gas zu schaffen, wenn es verschiedene Grundflächen gibt.
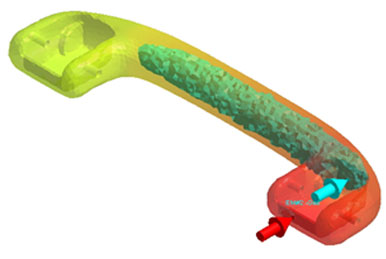
MuCell EINSPRITZUNG MIT MIKROZELLULARER AUSDEHNUNG
Das Spritzgießen mit der MuCell-Technik mit mikrozellularer Ausdehnung ist eine relativ moderne, aber bereits weit verbreitete Technik zur Herstellung von Teilen aus polymerem Material. Die innovativen Aspekte dieser Technik ergeben sich aus der Vermischung von Polymer und Inertgas direkt im Einspritzzylinder. Sobald das Gemisch den Formhohlraum erreicht hat, neigt das Gas dazu, sich auszudehnen, was zu einer Gewichtsreduzierung führt, da die Dichte des Gases geringer ist als die des Polymers, und zu einer Verformung, die eine gleichmäßige und kontrollierte Schrumpfung des gesamten Teils zur Folge hat: Bei den herkömmlichen Formverfahren wird die Abkühlung durch die von der Presse ausgeübte Wartung gesteuert, aber Schwankungen in der Länge des Flusses können zu Inhomogenitäten führen, die Verformungen, Absaugungen und andere charakteristische Defekte verursachen, während diese Probleme mit dieser Technologie erheblich reduziert werden.
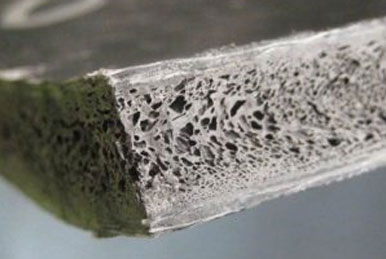
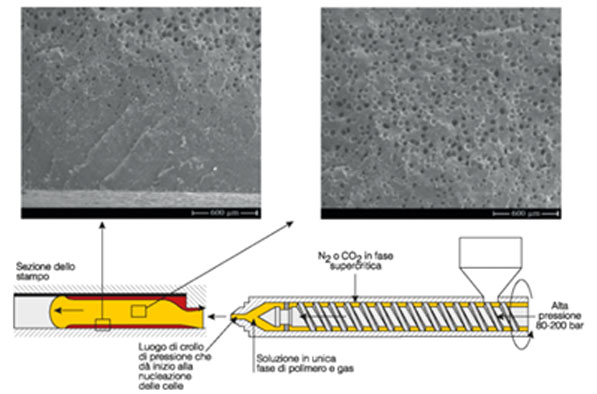
Vakuumhärtung
Die Wärmebehandlung von Härtungsstählen erfolgt durch Erhitzen des Materials über die Austenitisierungstemperatur und anschließendes abruptes Abkühlen unter Verwendung von Abschreckmitteln, um eine martensitische Struktur zu erhalten. Martensit hat eine hohe Härte und eine hohe Zugfestigkeit, aber ein geringes Rückstellvermögen, das es extrem spröde macht. Aus diesem Grund werden im Anschluss an die Härtungsbehandlung eine oder mehrere Anlassbehandlungen durchgeführt, die das Material unter den Ac1-Punkt erwärmen und so verhindern, dass es übermäßig spröde wird und Risse und Brüche in der Form entstehen. Die Kombination aus Härten und Anlassen wird als Anlassen bezeichnet. Insbesondere die Vakuumhärtung (ca. 10-3 bar) wird durch Erhitzen des Materials in einem Temperaturbereich zwischen 800 und 1200°C, basierend auf dem Kohlenstoffgehalt, und Einleiten von Stickstoff bei einem Druck zwischen 2 und 12 bar erreicht. Diese Behandlung ermöglicht es, isotrope martensitische Strukturen mit hohen Festigkeitswerten und geringen Verformungen zu erhalten, obwohl ihr im Allgemeinen eine oder mehrere Anlaßphasen folgen. Die Untersuchung der charakteristischen Abkühlungskurven des Materials, der chemischen Zusammensetzungen und der Dicken der betroffenen Teile ist unerlässlich, um ein korrekt gehärtetes Bauteil bis zum Kern zu erhalten und so Widerstandsprobleme und heterogene Verformungen zwischen verschiedenen Zonen zu vermeiden.
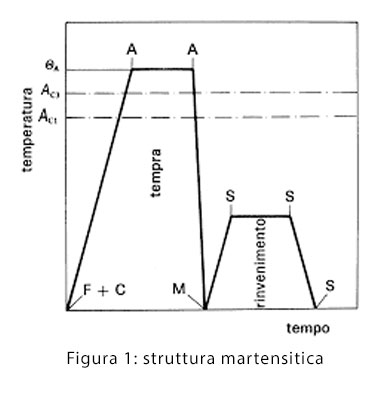
Gasnitrieren
Die thermochemische Nitrierbehandlung von Stählen ist ein industrielles Verfahren zur Oberflächenhärtung, das bei einer Temperatur von ca. 520-540°C durchgeführt wird und durch die Bildung von Nitriden erreicht wird. Insbesondere das gasförmige Nitrieren basiert auf der Ammoniak-Dissoziationsreaktion, die von Stahl katalysiert wird:

Bei dieser Reaktion entsteht atomarer Stickstoff, dem es gelingt, in die kristalline Oberflächenstruktur des Stahls einzudringen, die Löslichkeitsgrenze zu überschreiten und eine Härtung durch die Bildung von Nitriden zu bewirken.
Nach der Nitrierbehandlung bilden sich im Stahl verschiedene Zonen:
- Weiße Decke: eine von Nitriden gebildete Oberflächenzone, welche die Diffusion von Stickstoff in die Metallmatrix ermöglicht. Sie ist in der Regel sehr spröde und kann durch einen Schleifvorgang entfernt werden;
- Diffusionszone: Zone, die durch die Diffusion von Stickstoff gekennzeichnet und am stärksten von der Aushärtung betroffen ist;
- Übergangszone: Zone, die nur geringfügig von der Diffusion betroffen ist und den Übergang zwischen der Diffusionszone und dem Grundmaterial darstellt.
Das Nitrieren härtet den Stahl nicht nur, sondern erhöht auch seine Widerstandsfähigkeit gegen Verschleiß, Ermüdung und Korrosion (insbesondere mit einer zusätzlichen Nachoxidationsbehandlung). Außerdem handelt es sich um eine Behandlung, die je nach Zeitplan und Parametern des Ofens unterschiedlich tief in den Stahl eindringen kann. Die klassischen Komponenten, die einer Oberflächen-Nitrierbehandlung unterzogen werden, sind Formteile und Dübel, während gleitende Komponenten wie Führungen einer Tiefen-Nitrierbehandlung unterzogen werden.
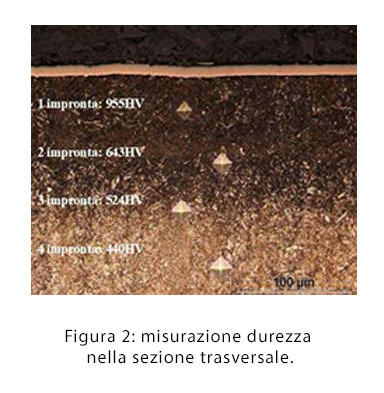
Karbo-Nitrierung
Die thermochemische Behandlung der Karbo-Nitrierung ist ein metallurgischer Prozess, der durch die Diffusion von Kohlenstoff und Stickstoff im Stahl gekennzeichnet ist. Es handelt sich um eine dem Aufkohlen ähnliche Behandlung, die allerdings bei niedrigeren Temperaturen (zwischen 720 und 910°C) durchgeführt wird und eine geringere Verformung aufweist, aber durch die Anwesenheit von Ammoniak mit Stickstoffdiffusion gekennzeichnet ist, was zur Bildung einer deutlich gehärteten Oberflächenschicht führt. Für eine wirksame Behandlung geht ihr in der Regel eine Entspannungsphase voraus, um Restspannungen zu beseitigen. Der Hauptvorteil dieser Art von Behandlung besteht darin, die Verschleißfestigkeit des Materials zu erhöhen, vor allem im trockenen Zustand. Aus diesem Grund wird sie bei Wellen, Zahnrädern und Kolben angewendet. Manchmal wird nach dem Kohlenstoffnitrieren eine Anlaßphase durchgeführt, um die Sprödigkeit des Stahls zu minimieren und Risse und Brüche zu verhindern.
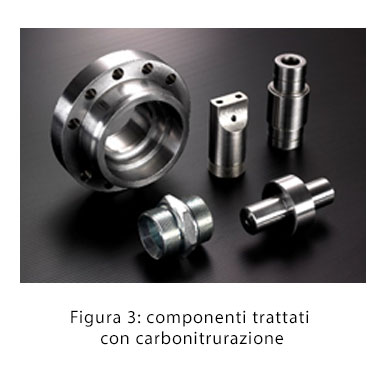
Alterung
Die Wärmebehandlung der Alterung wird auch als 'Ausscheidungshärtung' bezeichnet und ist eine Behandlung, die normalerweise nach dem Härten oder Lösungshärten durchgeführt wird. Durch diese Phasen, die durch abrupte Abkühlung gekennzeichnet sind, wird das Einfrieren der Struktur induziert und die Diffusion chemischer Elemente gehemmt. Nach der Abkühlung setzt bei Raumtemperatur ein natürlicher Alterungsmechanismus ein. Es ist jedoch auch möglich, das Material zu erwärmen, indem man eine künstliche Alterung herbeiführt, die zur Keimbildung und zum Zusammenwachsen von Partikeln führt (die je nach Phase kohärent oder inkohärent sein können). Diese Aggregate wirken als Hindernisse für die Bewegung der Versetzungen. Sie erfordern größere Anstrengungen, um Verformungen zu erzeugen, und härten so das Material: Um diese Teilchen zu überwinden, müssen die Versetzungen nach dem Scher- oder Orowan-Mechanismus Energie aufwenden.
Ein wichtiger Aspekt dieser Behandlung ist die Kontrolle der Zeit-Temperatur-Kopplung: Zu lange Erhitzungszeiten kommen dem Material nicht zugute, sondern führen zu einer "Überalterung" mit übermäßiger Partikelgröße und einer Verringerung der Härte gegenüber dem optimalen Wert.
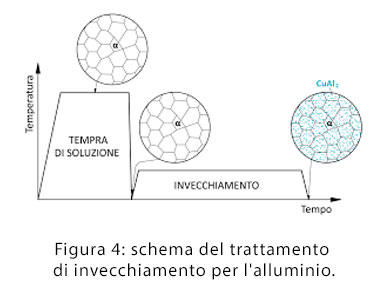
Oxidation
Die chemische Behandlung der Oxidation zielt auf den Oberflächenschutz des Metallmaterials durch die Ablagerung einer Oxidschicht ab, die als Schutzschicht fungiert und den Angriff durch atmosphärische Einflüsse verhindert, die Spannungen oder Korrosionserscheinungen hervorrufen können. Darüber hinaus kann die gebildete Oberflächenschicht später als Substrat für das Auftragen von Farben oder anderen Beschichtungen dienen. Die verschiedenen Arten der Oxidation unterscheiden sich durch ihre Oberflächenfarbe, ihre Dicke (einige bilden sich an der Oberfläche, andere dringen in den Stahl ein) und andere chemische und physikalische Eigenschaften.
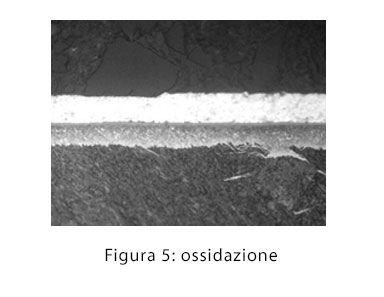
Spannungsarmglühung
Die Spannungsarmglühung wird durchgeführt, indem der Stahl auf eine Temperatur unter Ac1 erhitzt und dann langsam auf Raumtemperatur abgekühlt wird. Der Zweck dieser Behandlung besteht darin, die durch die vorangegangenen Produktionsschritte erzeugten Spannungen zu beseitigen, ohne die Härte zu verändern, und so Verformungen zu verhindern, die in den nachfolgenden Schritten auftreten können. Außerdem wird die Abkühlung in einem Ofen oder an der Luft über einen längeren Zeitraum durchgeführt, um weitere Spannungen im Material zu vermeiden.
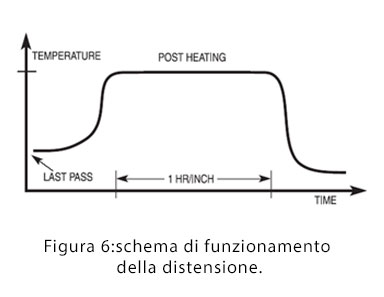
Spannungsarmglühung nach der Oxidation
Die beschriebene Spannungsarmglühung kann durch eine chemische Nachoxidationsbehandlung ergänzt werden, welche die Korrosionsbeständigkeit erhöht und die Ablösung des Aluminiumdruckgusses vom Formstahl fördert. Die Nachoxidation ist eine Art der Behandlung, die auch am Ende des Nitrierens mit Luft, Distickstoffoxid (N2O ) und Kohlendioxid (CO2) durchgeführt werden kann. Die wichtigsten Vorteile sind:
- Erhöhte Korrosionsbeständigkeit;
- Verbesserte Verschleißfestigkeit;
- Ausgezeichnete Oberflächengüte.
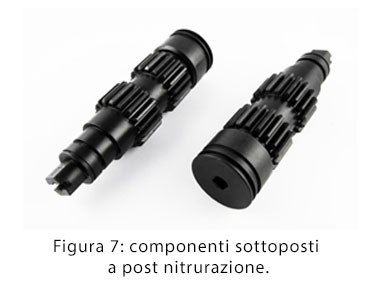